This is a continuation of the
Process Intensifier - Optimization with CFD: Part 1 paper.
Residence Time Distribution
Residence time is computed using Lagrangian analysis particle tracking
procedures within the resultant flow state. The tracers are assumed to be
neutrally buoyant and convected along by the flow. That is, that the tracers do
not influence the flow field. This class of analysis by definition applies to
discrete particles and not continuous flow characteristics. Two classes of
analysis are done in this fashion, which include extracting particle path
information along with a variant on Poincare analysis looking at plane
intersections for the determination of residence time. The plane intersections
provide this residence time by recording the time, position, velocity, and a
number of other variables as a particle intersects a specified plane. The
standard interpretation of Poincare planes is that they are applied in mixing
tanks to collapse time out of the analysis. Data extracted from plane
intersections can be subsequently studied by a variety of statistical means
looking at min, max, average, median, and a variety of other statistical
measures.
Residence time statistics are handled from the injection point to a vertical
plane at 35 inches (900 mm) down stream from the impellers. In the case of the
radial impellers, the injection point is exactly below the lower impeller. In
the case of the HGA the injection point is from that pipe between the criss-cross
flow straighteners and the impeller shaft, which is 4 inches (100 mm) upstream
of the shaft. For the LTA, the injection point is 35 inches (900 mm) up stream,
either at the center of the pipe or split into two feed locations at the
respective heights of the axial impellers.
1250 tracer particles were used in each CFD experiment of Table 6. LTR, HGR,
and HGA had two injection ports. For these 625 tracer particles were used
through each port. LTA had a singular port and so all 1250 tracer particles went
through that port. The LTA - Split Injection case had two injection ports at the
respective height of the impellers. Figures 19 - 20 show the results
graphically.
The time scales of Figures 19-20 are logarithmic so that more detail can be given to the shorter times.
Model |
LTR |
LTR |
HGR |
HGR |
HGR |
LTA |
LTA |
LTA |
LTA |
LTA |
HGA |
HGA |
Q |
650 |
1100 |
650 |
1100 |
750 |
650 |
650 |
1100 |
1100 |
1100 |
650 |
1100 |
N |
1750 |
1750 |
1750 |
1750 |
1500 |
1750 |
1750 |
1750 |
0 |
1750 |
1750 |
1750 |
Info |
|
|
|
|
Non-Newtonian |
|
Split Injection |
|
|
Split Injection |
|
|
|
Min |
0.48 |
0.57 |
0.39 |
0.35 |
0.41 |
1.76 |
1.87 |
1.13 |
1.09 |
1.08 |
0.77 |
0.46 |
Max |
10.66 |
6.01 |
6.22 |
34.09 |
4.91 |
5.27 |
5.15 |
4.02 |
1.87 |
3.23 |
3.53 |
2.00 |
Spread |
10.17 |
5.45 |
5.83 |
33.73 |
4.50 |
3.51 |
3.28 |
2.89 |
0.78 |
2.16 |
2.76 |
1.54 |
|
Mean |
1.35 |
0.80 |
1.27 |
0.75 |
1.10 |
2.26 |
2.26 |
1.34 |
1.34 |
1.34 |
1.27 |
0.75 |
Median |
1.57 |
1.30 |
1.21 |
1.02 |
1.15 |
2.15 |
2.29 |
1.16 |
1.19 |
1.31 |
1.36 |
0.77 |
Ave |
1.89 |
1.46 |
1.54 |
1.16 |
1.37 |
2.27 |
2.46 |
1.19 |
1.20 |
1.42 |
1.41 |
0.81 |
STD- |
0.78 |
0.84 |
0.53 |
0.04 |
0.62 |
1.92 |
1.95 |
1.04 |
1.14 |
1.13 |
1.03 |
0.60 |
STD+ |
3.00 |
2.09 |
2.55 |
2.28 |
2.11 |
2.61 |
2.97 |
1.34 |
1.27 |
1.71 |
1.78 |
1.03 |
|
STD |
1.11 |
0.62 |
1.01 |
1.12 |
0.75 |
0.34 |
0.51 |
0.15 |
0.07 |
0.29 |
0.37 |
0.21 |
VAR |
1.23 |
0.39 |
1.01 |
1.25 |
0.56 |
0.12 |
0.26 |
0.02 |
0.00 |
0.08 |
0.14 |
0.05 |
SKEW |
2.81 |
0.51 |
1.44 |
32.25 |
0.55 |
0.08 |
0.25 |
0.04 |
0.00 |
0.04 |
0.05 |
0.01 |
Table 6: Statistics of the residence time distributions
of all systems tested. With the exception of VAR (variance) and SKEW all the
other statistical numbers are in time units of seconds. The Mean is based on
the volume and the volumetric flow rate that the tracers passed through. The
flow rate, Q, is in GPM. The impeller speed, N, is in RPM. |
650 GPM |
Radial Process Intensifier |
Axial Process Intensifier |
Lightnin |
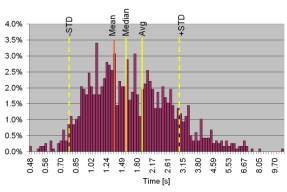 |
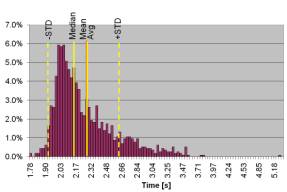 |
|
LTR |
LTA |
Hayward Gordon |
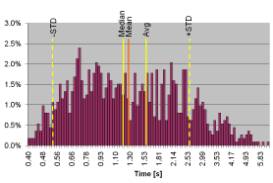 |
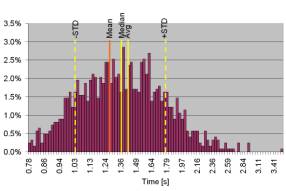 |
|
HGR |
HGA |
Figure 19: Residence Time Distribution Plots for 650
GPM (148 m3/hr). |
1100 GPM |
Radial Process Intensifier |
Axial Process Intensifier |
Lightnin |
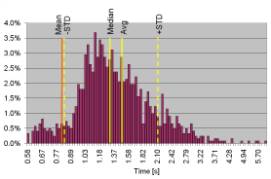 |
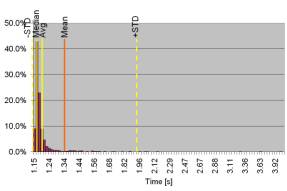 |
|
LTR |
LTA |
Hayward Gordon |
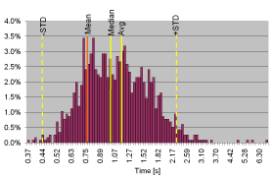 |
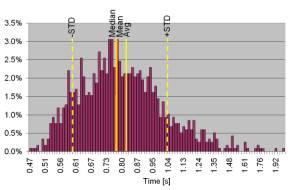 |
|
HGR |
HGA |
Figure 20:Residence Time Distribution Plots for 1100 GPM
(250 m3/hr) |
Even though the Radial Process Intensifiers are fairly similar, the residence
time distributions (RTD) are slightly different and show that they are not alike
(Figures 19-20). At 650 GPM (148 m3/hr), each impeller develops at least 50%
more flow than the overall throughput flow (Table 5). The RTD of the LTR is more
normally distributed than the HGR, even though the spread of the tracers is
wider for the LTR. The HGR has almost an even distribution of times through
itself. The RTD is quite flat. In both cases about as many tracers go through
the unit faster than the mean as are retained longer. This is illustrated in
Figures 17-18. At 1100 GPM (250 m3/hr) both of them have more particles getting
trapped in recirculation areas and are retained longer than the mean. At the
higher flow rate, the HGR does a better job, even though the STD of LTR is much
tighter. Almost all tracer particles are retained longer than the mean flow.
This is actually quite amazing and shows that the tracer material will be longer
mixed with the fluid around it before leaving the Process Intensifier in a
fairly tight band. To help these two units, the injection of the second
component should be at a better spot (see Part 2).
The Axial Process Intensifiers are not similar at all, which was to be
expected from the previous discussions. The LTA can barely affect the RTD,
whereas the HGA is doing a very good job at both flow rates. Figure 17 does show
distribution of particles and the RTD plot does show that more than half of the
particles do come out after the mean. Figure 18 also reflects the more uniform
distribution as seen here. The difference has a lot to do with the point of
injection (discussed later).
At both pipe flow rates, the majority of the tracer particles from LTA travel
through the pipe faster than the mean flow. This is not good and indicates that
the tracer particles are indeed by-passing the impellers. At 650 GPM (148
m3/hr), there is some retention of the tracers (about 40%) indicating that the
impellers are doing something. Figure 17 shows that much of them do continue
right through the middle, between the two impellers. At the higher flow rate,
1100 GPM (250 m3/hr), the LTA is totally overwhelmed. Figure 20 shows the
tightest RTD of them all, and it is the worst mixing. Notice that there are a
few tracer particles that do come in after the mean. These are tracer particles
that were probably lucky enough to hit the shaft on the way. Otherwise
essentially all of the tracer particles traveled pass the impellers without
noticing them.
It is often said that a tight residence time distribution is desirable
because all particles will "see" the same environment. A certain
spreading of the residence time distribution is obviously necessary in a
pipeline so that axial (or backmixing) is possible. Otherwise slugs of
concentration gradients can be traveling through the pipeline. Furthermore, it
appears that a tight RTD after the mean is ideal.
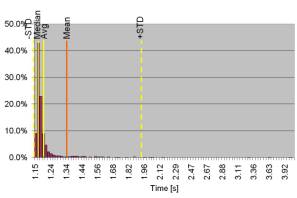 |
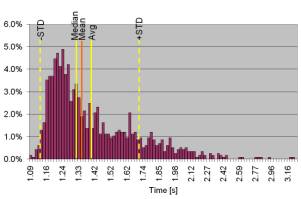 |
LTA – 1100 GPM – 1750 RPM – Single |
LTA –
1100 GPM – 1750 RPM – Dual |
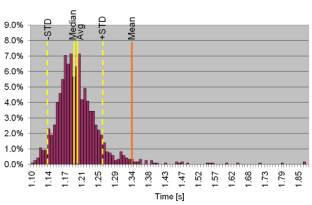 |
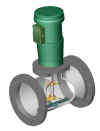 |
LTA – 1100 GPM – 0 RPM - Single |
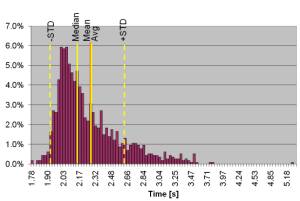 |
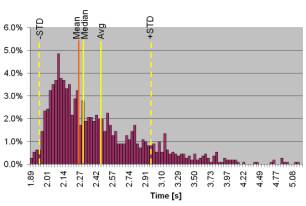 |
LTA – 650 GPM – 1750 RPM – Single |
LTA – 650 GPM – 1750 RPM – Dual |
Figure 21: Residence Time Distribution Plots for
LTA |
Because the LTA did so poorly (especially at 1100 GPM (250 m3/hr), we decided
to try another injection mode. By doing something similar to HGA, we injected
the tracers at the respective heights of the impellers (Dual), but at the same
location as the singular injection (single). This way, the flow will bring the
tracers to the impellers instead of bypassing them completely. Figure 21 shows
the RTD results at both flow rates
At 1100 GPM (250 m3/hr), the improvement is remarkable. Still the majority of
the tracers go through the pipe faster than the mean, but about 50% of the
particles are retained longer. This illustrates the importance of optimization.
The little alteration did not cost any more power to achieve this better result.
Even at the lower flow rate of 650 GPM (148 m3/hr), the retention of tracers is
much better and more than 50% of them are passing through slower than the mean.
Since the power for this device is so low, this would be an ideal pipe mixer for
fairly easy components to mix. With the right impeller placement, two or three
of these in series would do an excellent job and still use less overall power
than any of the other units. Injection closer to the impellers, like HGA,
probably would even do a better job (see Part 2).
The middle plot in Figure 21 is the LTA without spinning (N=0 RPM). Even
though the RTD looks very different than the RTD of LTA at N=1750 RPM, they are
essentially the same, with the exception of a few stragglers at 1750 RPM. They
probably got stuck somewhere or were lucky enough to hit the shaft. Both of them
have the first particle coming through in about 1.1 s and the last one (with
exception of those stragglers) at about the mean, which is 1.34 s. In other
words, without the dual injection ports, the LTA could just as well be turned
off.
Continue with Shear Rate Distribution (SRD)
or
Go back to Results
or
Go back to the Title Page
|