This is a continuation of the
Process Intensifier - Optimization with CFD: Part 1 paper.
The eddy viscosity can be understood to be an indication of a turbulence magnifier. Looking at relative magnitudes of this value give an indication of the level of turbulence contained within the enclosed volume. What becomes important is the size and magnitude of the volume. For this study, the 50% level of eddy viscosity was arbitrarily chosen as a discriminator to illustrate a concept. Hence, the iso-surface corresponding to that value was determined. It should be realized that contained within this volume is a higher turbulence measure, and outside the volume is lower. The implication to mixing becomes the size of the volume relative to how long particles are resident within.
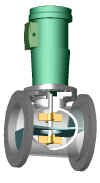 |
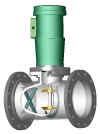 |
 |
 |
 |
 |
 |
 |
 |
 |
HGR – 650 GPM – 1750 RPM – Water |
HGA – 650 GPM – 1750 RPM – Water |
Figure
23: Characteristics of the HGR and HGA: Velocity vectors, mixing
tracers, eddy viscosity, and RTD plots. Internals other than the
impellers and shaft are not shown. |
Figure 23 shows 4 different types of plots. The top and bottom ones have already been discussed. The second set is "mixing" tracer plots. Two sets of discrete tracer particles are injected to see how them mix. The blue comes from the beginning of the pipe and are uniformly distributed, just like the flow pattern tracers above. The green particles are added at the respective injection port. In the case of the HGR, it was below the lower impeller. In the case of the HGA, it was injected through a pipe just in front of each impeller. The colors this time have nothing to do with residence time. In both cases there is a fairly good mixture of these particles.
The 3rd set is the Eddy Viscosity plots. The light green object is the iso-surface of Eddy Viscosity. Everything inside the surface has a higher Eddy Viscosity and everything outside it will be less. The eddy viscosity has the same units as the kinematic viscosity, m2/s. This value when multiplied by the proper (Reynolds averages Navier Stokes - RANS) strain rate tensor produces the amount of "Reynolds shear" attributed to turbulence and then applied in the momentum equation (this is a very loose interpretation).
|